Station building
Design of Diaphragm and Pile Wall Stations in Metro Line 4
Mining Method
Cut-and Cover Method
1. Diaphragm Wall
2. Bored Pile
Enclosure of Pit by Secant Piles and Pile Wall
3. Metro Stations designed using diaphragm and pile wall technology
4. "Top Down", "Milan" or "Deckel-Bauweise" method (diaphragm wall + slab, pile wall + slab)
5. Construction Method using Sloping Pile Wall
6. Two-Phase Slab Construction Divided into Transversal Sections, with Central Construction Joint
Stations and Wayside Engineering Structures, Headshunt-Reversing Facility
Design of Diaphragm and Pile Wall Stations in Metro Line 4
Several factors exist to define the building technology of underground constructions. In addition to geological and hydrological viewpoints (soil structure, soil strength, permeability, ground water condition etc.), important factors are geometry and location of the facility (bottom depth, soil layer above floor). A decisive issue is the impact of the building technology selected on the built and natural environment. Its impact on human environment in densely built urban zones shall not be neglected either. Correct selection of the building technology is important due to construction-related settlements and pervasive building risks.
When selecting building technology and aiming at the least possible risk, it is necessary to assess all known influencing factors, considering the viewpoints of functionality and efficiency.
In theory, metro stations, reversing structures and head-shunts may be implemented both by cut-and-cover and mining construction methods, if considered independently of their environment.
Mining Method
The mining method can be either traditional or modern shotcrete method using explosives or mechanical tunnel boring. When building longer sections it is more economical to work with tunnel driving machine (road header), open or closed-front tunnel shield and, in rocks of high strength, with tunnel boring machine.
The advantage of the mining method is quite obvious in the case of long underground structures, running tunnels, larger soil covering and densely built-in urban districts.
Using a modern, closed bentonite sludge slurry-shield or earth pressure balance (EPB) shield, nowadays tunnelling is also possible under small soil covering.
Cut-and Cover Method
Using cut-and-cover method the engineering structure can also be built in sloping working pit, however, this is not possible under urban conditions. In such an environment only working pits with vertical walls are conceivable, such as supported by sheet-piles, diaphragm wall and bored pile.
In the course of supporting the pit by beaten or vibrated sheet-pile walls, this method may impose considerable noise and vibration on its environment. Such support structures of working pits implemented by environment friendly construction, of suitable desing and watertightness, may also act as load-bearing structures of underground facilities.
Working pits constructed using diaphragm or pile wall technology, provided they are combined with proper propping or anchoring, do not cause any considerable settlement in their environment.
1. Diaphragm Wall
Diaphragm wall is an under-surface structure which is constructed nowadays with special electronically controlled machine and clamshell attachment, specifically, diaphragm wall technology. Wall thickness is quite insignificant with respect to its depth, thus, the obtained working pit is a narrow gap. Side walls of this gap are supported by sludge having a density superior to that of the water. Prefabricated, welded steel reinforcement is placed into this gap. Concrete is poured into the diaphragm wall under the protection of this dense sludge, under sludge level, progressively pulling out the concrete pumping pipe. Practically, the thickness of such a diaphragm wall ranges from 0.6 m to 0.8 m, its depth may be up to 40 m.
Enclosure of Pit by Diaphragm Wall
Several diaphragm wall panels may be close to one another, thus, by combining an arbitrary number and shape of diaphragm wall panels, the side walls of an underground engineering structure of proper geometry can be implemented. If individual panels are made using sectioning pipes, then such panels can be constructed intersecting and attaching to one another at the place of the extracted sectioning pipes, and finally a reinforced concrete structure can be obtained. In order to enhance watertightness, a special expansion strip is placed between the joints of panels, thus, a watertight working pit is obtained, a so called "white bathtub".
2. Bored Pile
Bored piles are underground structures constructed by boring technology. The large diameter bore for such piles are made with special electronically controlled driving machines. The selection of specific boring tools (spiral, bucket, roller etc.) depends on soil characteristics.
In general, bore holes are protected against colapse by sleeve pipes, the earth being removed from inside sleeve pipes with proper tools. Having reached the depth envisaged, the so called armature (prefabricated welded rebar structure matching the bore size) is sunk and filled with concrete under the progressive pulling out of sleeve pipes.
Enclosure of Pit by Secant Piles and Pile Wall
A pile wall can be formed by piles bored close to one another. In order to ensure watertightness the piles are located in a manner to have a lower spacing than their diameter, i.e. the piles intersect one another. They can be referred to as intersecting piles.
The newly-completed non-reinforced concrete piles can be bored, while the reinforced ones cannot be bored. That is why it is important to keep the order in a bored pile wall. Reinforced piles are always bored between two previously completed, non-reinforced concrete piles, then continuing alternatively with reinforced and non-reinforced ones, length and shape as necessary. Practically, pile diameter ranges from 0.9 to 1.2 m, its length is optional.
By boring an arbitrary number of piles near one another, an intersecting (secant) pile wall can be obtained. The working pit supported by pile wall made by this technology is laterally watertight.
When constructing pile walls no rock deformation is cause to its environment, no significant settlement occurs whatsoever, since the hole bored is supported by concrete in each moment of the construction.
3. Metro Stations designed using diaphragm and pile wall technology
Considering many different viewpoints, alignment of Metro 4 was set out to locate stations under large squares and streets. This solution is more economical, more passenger friendly, and more favourable in terms of passenger traffic, since the stations can be at a higher level, transfer time is shorter and, consequently, the travel time can be reduced.
The stations located at a higher level and the open squares above them enable cut-and-cover technology using diaphragm walls or pile wall.
The top slab is made on the top of the watertight box structure made of pile walls or diaphragm walls, and the base slab is constructed underneath at the designed depth. In this manner, a rough reinforced concrete structure is obtained for box stations, comprising an arbitrary number of intermediate floors according to the depth.
Cut-an-cover methods are difficult to be used in dense urban environment. During construction it can occupy an important surface area to the detriment of traffic, and can be harmful due to noise and dust generation. However, several versions are already known to reduce environmental damages.
In the course of construction an organisation and construction order should be selected to achieve the smallest possible building area and shortest time, being the main factors in surface problems.
In the countryside and cities where metro is being constructed for a long time and in a continuous manner, many valuable experiences have been gathered and environment friendly construction technologies applicable in city centres have been developed.
Such a construction technology is the so called "Milan Method" or in Germany the "Deckel-Bauweise" (= top slab construction), i.e. "Top-Down" construction method.
Watertight working pit enclosures with long diaphragm walls or pile walls can interfere with external, natural ground water flow. In order to compensate backwater effect using a monitoring system for ground water, properly sized transfer structures or systems are constructed, which have provided good results in practice. Such structures also function well along the North-South Metro line, in parallel to the Danube. It is significant with regard to the long head-shunt structure near Thököly út metro station, however, the headshunt is nearly parallel to the main ground water flow direction therefore the backwater effect is not so significant.
4. "Top Down", "Milan" or "Deckel-Bauweise" method (diaphragm wall + slab, pile wall + slab)
In this method it is essential that the top slab is made first, then the construction of stations is continued under this slab by mining method with less problems caused to the environment or surface.
This is a method also applicable in the construction of box stations of Metro 4. In the first phase, diaphragm walls or pile walls are made at the side of stations, with continuous maintenance of traffic, if possible. Utility relocations should be made section by section, in order to ensure problem-free operation. The works should be organised in a manner to have access to residential houses and shops at all times. Ambulance, fire service, garbage collection, goods supply should be continuous, no obstacle is allowed along the route for the handicapped or baby carriages. Such conditions should be planned before commencement of construction and relevant official authoriity approvals shall be obtained.
Following the construction of diaphragm walls or pile walls, a top reinforced concrete slab is constructed, using formwork placed on the ground. All final utilities can be replaced on the top slab completed in this manner and final surface traffic order can be restored, as well as surface facilities can be used again by car or pedestrian traffic. This means a minimum construction time when all problems associated with construction should be tolerated by the environment and population. In narrow streets local traffic can be directed to a temporary road surface placed on consoles attached to diaphragm or pile walls. Thereupon, station construction is continued under the slab. Earth removal under the top slab is made by mining method, according to local conditions, through an opening left in the slab, or through a transport tunnel located farther, or even through a shaft built near the station. For station construction works such openings or tunnels can also be used.
The supply openings can be closed by noise protection covers overnight. Thus, the work can be continued day and night, which is a pre-condition for fast and efficient metro construction. Ventilation in the closed station area is provided by fans, through pipes and dust separator.
Earth removal from under the slab has some disadvantages as well: specific earth removal is slower, lighting and ventilation should be provided. On the contrary, thanks to the several workshifts, the total construction time can be considerably reduced. Thanks to this construction method, no expensive and time-consuming auxiliary structures or anchors are required, instead intermediate slabs are made for ensuring propping between diaphragm or pile walls.
5. Construction Method using Sloping Pile Wall
Underground lines are being built today not only in cities like Budapest, but also in historical centers of smaller towns. Narrow streets and small squares of such towns do not enable to separate large station areas from the surface.
However, technical development yielded the electronic control of various machines, including building machines. Thus, structures of higher accuracy can be produced. This was the basis of constructing watertight sloping pile walls of large diameter, exactly intersecting reinforced concrete piles.
Station areas with required platform width can be developed in this manner under narrow surface streets, by means of sloping secant pile walls bored outward from street axis.
The stations constructed in this manner are narrow at the top and become wider and wider towards the bottom. Thus, engineering structures can be designed more economically, since the box structure of stations should not be adjusted to various facilities at the top.
In case of pile walls made of sloping driven piles, the surface slab system is narrower, the enclosed building area will be smaller as well,, and a large surface area is left to the transport and surface users.
Combination of the building technology with sloping pile walls and the Milan method is an ideal solution for the construction of stations, engineering structures inside central urban zones.
6. Two-Phase Slab Construction Divided into Transversal Sections, with Central Construction Joint
Several modern building structures and auxiliary procedures have recently been developed and applied for the construction of underground engineering structures and metro stations within the center of historical cities and in narrow downtown streets. With this in mind, even previously inconceivable situations can be resolved. It is possible to build a top slab in two phases, with transversal construction sections and central construction joint. Thus, one building phase takes even less surface area from the traffic, it is advantageous for utility relocation and reinstatement, as well as in congested central urban areas and for the temporary traffic diversion.
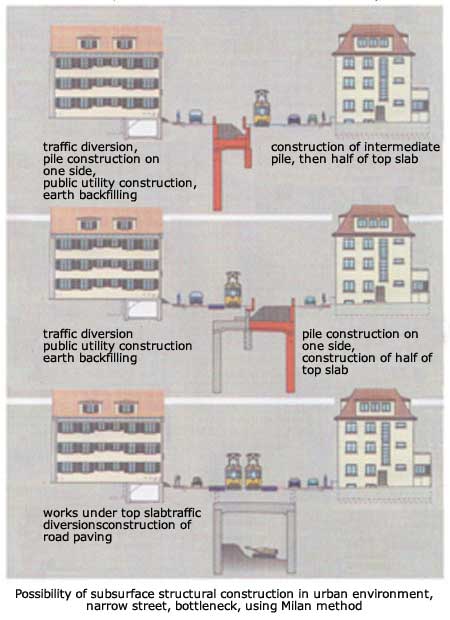
By applying the building method using diaphragm or pile walls for the enclosure of working pits, as well as the "Milan method" as suggested above, the construction period disturbing surface activities can be reduced to as much as 6 to 8 months per metro station. This is indispensable, since it is inadmissible among the existing viewpoints of city operation and human interests to close an important Boulevard in the city for several years, like it was the case at lli t and Vci t - twenty years ago.
Stations and Wayside Engineering Structures, Headshunt-Reversing Facility
- Kelenföld pályaudvar Station shall be located under MÁV railway station, thus, only mining method can be used.
- The location of two stations is influenced by the Danube. Szent Gellért tér Station is partly under the building CH of the Technical University, and Fővám tér Station partly under the Danube, respectively. Station structures under this building and the Danube can be constructed only by mining method.
- Móricz Zsigmond körtér Station, due to a sufficient soil covering, can also be constructed by mining method, as an alternative.
- The mining method for the rest of stations is only possible using expensive complementary and soil improving auxiliary works, like soil strengthening, overpressure, or dewatering within a "watertight box" constructed from the surface using injected waterproofing walls, soil freezing or even their combination.
- Népszínház utca Station and Keleti pályaudvar Station can economically be constructed only from the surface, by cut-and-cover method, since the works should be carried out in Pleistocene sand or sandy gravel layers.
- The headshunt and reversing structure at the Baross tér can also be constructed using diaphragm or pile wall.